Belt conveyors are widely used in factories, mines, and logistics centers.
One critical design factor is the "trough angle." This article explains what the trough angle is, the benefits and issues of increasing it, and how to choose the right angle for your needs.
目次
1. What Is Trough Angle?
The trough angle refers to the angle formed by the rollers (idlers) that support the conveyor belt.
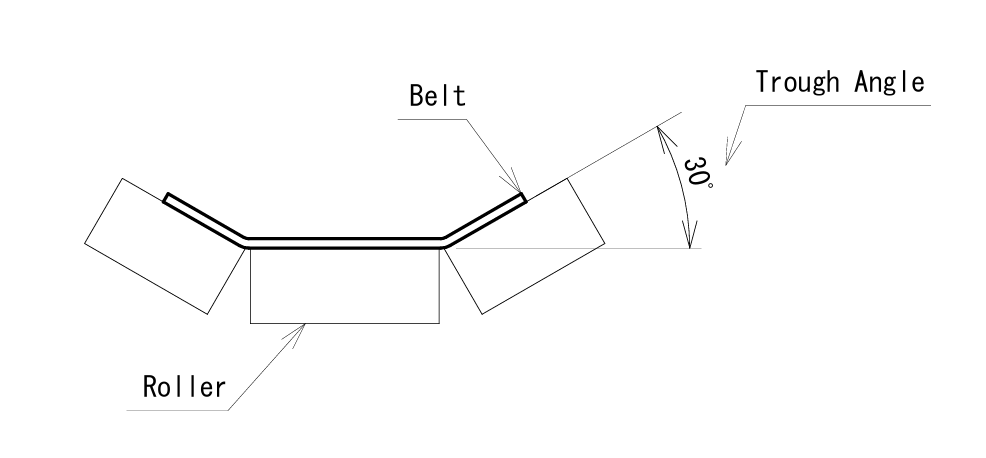
These rollers shape the belt into a U-like cross-section, helping to contain the conveyed material. Typical trough angles include:
Trough Angle (°) | Applications |
---|---|
20° | Small conveyors, general items (boxes, pallets) |
30° | Common bulk materials (powders, granules), standard conveyors |
35° | Large volume transport (ore, coal, gravel) |
40°+ | Long-distance or high-capacity conveyors (custom design needed) |
2. Benefits of Increasing the Trough Angle
Increased Conveying Capacity
Larger trough angles allow the belt to hold more material by increasing its cross-sectional area.
This enables higher transport volumes in the same footprint.
Reduced Spillage of Fine Materials
The raised belt edges prevent material—especially fine or granular substances—from spilling, making it ideal for outdoor use or dusty environments.
Potential Energy Savings
By concentrating the load at the belt center, friction may be reduced, potentially lowering motor energy consumption.
3. Drawbacks and Issues with Larger Trough Angles
Increased Edge Tension
As the trough angle increases, so does the tension at the belt edges, which can lead to edge wear, cracks, and shortened belt life.
Risk of Material Blockage or Spillage
At loading or transition points, materials may clog or spill more easily due to the steep belt shape.
Belt Misalignment (Tracking Issues)
Larger trough angles may reduce belt stability, increasing the risk of misalignment or belt "tracking" problems. Additional tracking guides may be needed.
Heavier Load on Center Rollers
The central idler bears more weight, which can cause faster wear or damage, especially in long-distance conveyors.
4. How to Choose the Right Trough Angle
Balance is Key
- 30° is a standard angle suitable for many applications.
- 35°+ angles require careful consideration of belt strength, tracking systems, and maintenance.
- For long-distance or high-capacity conveyors, support devices like centering rollers or custom idlers should be installed.
5. Summary
Factor | Benefit | Drawback |
Capacity | Increased transport volume | - |
Dust Control | Reduced material spillage | - |
Energy Efficiency | Reduced motor load | - |
Belt Durability | - | Edge wear increases |
Material Flow | - | Higher chance of blockage or spillage |
Roller Load | - | Increased wear on center rollers |
Choosing the correct trough angle involves understanding your material properties and conveyor usage. A well-balanced design helps maximize conveyor performance and lifespan.
If you're looking for more tips and insights useful in mechanical design, feel free to check out our other articles and resources!
References
- JIS B 8805: Structure and dimensions of belt conveyors
- "Modern Belt Conveyor Design and Trouble Prevention" (Nikkan Kogyo Shimbun)
If you are unsure about selecting the right trough angle, don’t hesitate to consult with a conveyor equipment manufacturer or engineer!